One Talk
Cement supply, manufacture and sustainability ACTion newsletter
Welcome to the new online version of your Bulk Cement newsletter. Why not bookmark the page now for easy future access to the latest information from cement. Also, if you want to contact the team use one of the email contact options at the top of the page
What is cement doing to cut CO2 and achieve Net Zero?
Our new sustainability strategy was launched in October ‘21, it builds on this achievement. It is called Act because we firmly believe we all need to act now to change our future. It focuses on three key themes – People, Planet and Solutions – and underpins actionable priorities for the next decade and beyond.
We all get asked the questions about sustainability and clearly as a cement and lime producer we will see fundamental changes to all aspects of our industry over the coming years.
Today, there is much action and ambition to be proud of.
UK Concrete and Cement industry ‘Beyond Net Zero’ roadmap
Tarmac has been actively involved in the development the UK Concrete and Cement industry ‘Beyond Net Zero’ roadmap. The roadmap sets out how by 2050 the UK concrete and cement industry will not only achieve net zero carbon but go beyond net zero, to remove more carbon dioxide from the atmosphere than it emits each year. The key levers for decarbonisation include transitioning to renewable electricity, switching to lower CO2 waste-derived fuels, developing low carbon cement formulations and implementation of carbon capture use or storage (CCUS).
The roadmap highlights the steps industry will need to take and the policy and economic support measures needed from Government, including investment in enabling infrastructure like electricity grid capacity, hydrogen networks and CO2 transport and storage.
Actively, playing our part!
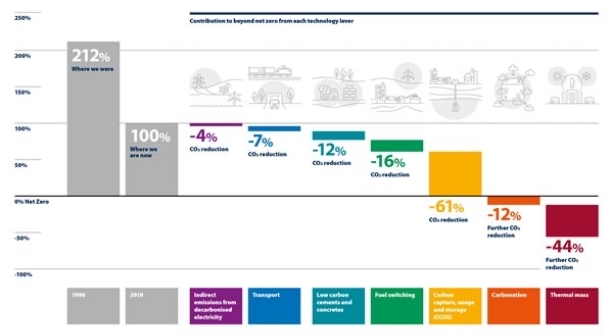
Using lower CO2 energy
We are committed to using lower CO2 fuels wherever this is technically and economically feasible.
Focus on energy
In 2020, over 41 percent of the heat input needed in our cement kilns came from waste-derived fuels, this included 13.6 percent from biomass. The types of fuels used across our cement operations now include waste tyres (whole or chipped), solid recovered fuel (SRF) from non-hazardous materials including paper, cardboard, plastics, textiles and waste wood chips, recycled liquid fuel, processed sewage pellets (PSP) and polymer chip. Fuels such as PSP are 100% biomass while tyres, SRF and polymer chip contain a proportion of biomass. The use of waste-derived fuels containing biomass makes a significant contribution to reducing CO2 emissions as waste biomass is considered carbon neutral.
Plasma energy and hydrogen technology innovation
During the year our business also stepped forward to take part in a ground-breaking project to explore the potential of plasma energy and hydrogen technology in the production of cement and lime. The research is being funded by the Department for Business, Energy and Industrial Strategy (BEIS). Tarmac’s Tunstead cement plant in Derbyshire will be host to some of the cement trials and will also be used to explore the viability of hydrogen as an alternative to natural gas for high calcium lime manufacturing.
100% renewable electricity
Our long-term power purchase agreement (PPA) with our electricity supplier ensures that 100% of the electricity we purchase across the whole of our business comes from a renewable energy source (a mix of wind and solar energy). This is backed up by Renewable Energy Guarantees of Origin (REGOs) to prove the electricity was produced only from renewable sources.
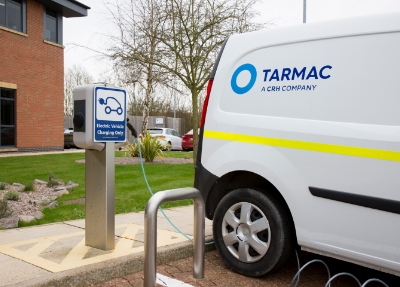
Low Carbon Innovation
CO2 in cement and concrete is commonly reduced by substituting the cement with a proportion of a secondary component, such as fly ash, blast furnace slag and limestone. Until recently these were limited by UK concrete product standards to just one type of addition to replace part of the cement.
EN 197-5, published in May 2021 has introduced two new ternary cement types, the Portland-composite cement CEM II/C-M, and the composite cement CEM VI. With the help of Government funding Tarmac is working with the MPA and the Building Research Establishment to amend the concrete standard, BS 8500, to recognise the use of these ternary cements in all durability and concrete design classes. It is anticipated the standard will be amended in early 2023. This will open the way for these lower carbon options to be used confidently by architects, specifiers and designers. For Tarmac Cement this will also require a move away from producing standard CEM I to offering a Portland Limestone Cement (PLC) CEM II/A-LL. CRH already has experience of such a change. In Ireland the standard changed 15 years ago and led to a wholesale move to PLC.
Clearly this will have major implications for all aspects of Tarmac’s concrete business. For us to be properly prepared Andy Campling, National RMX Technical & Business Optimisation Manager, is heading a multi-discipline project team. Its remit is to ensure we maximise the opportunity to reduce CO2 without compromising performance, have the capability to meet future market shifts and assess the commercial benefits we could derive. Several sites will be running extensive trials over the next six months using PLC, which is already available from our Aberthaw plant. These are: Wellington Blocks, Wellington RMC, Wincanton RMC and Briton Ferry RMC.
We’ll be providing regular updates on these trials over the coming months and more details of what is likely to be a major change in the cement market in the medium term.
Andy Campling comments,
“A group of colleagues across Cement, RMX and TBP are working on a carbon reduction trail by introducing PLC cement into RMX and Blocks.
The aim of the group is to understand the benefits for Tarmac of switching Bulk Cement from Cem I to Cem II A-L (Portland Limestone Cement) and develop in-house trials in RMX, Blocks and mortar, to establish the optimum Cem II product and develop a 2023-2025 roadmap for Cem II use in Tarmac.
Along with the cement performance and effect on RMX concrete strengths, there are also several areas which are being reviewed as part of the project, such as our operational requirements, storage, Bristish & European standards, and market demand. A subgroup has also started considering the use of Calcined Clay cements in the longer term.
The benefit of carbon reduction is significant across Tarmac, this is just one step to help achieve our aspiration.”
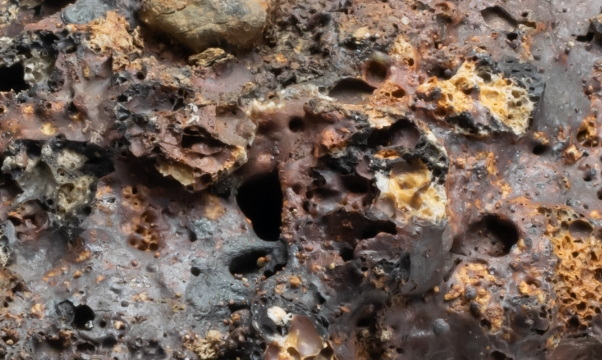
ACTion Cement
As you can see there is a tremendous amount of hard work and effort invested in ensuring Tarmac meets its sustainability commitments both in terms of cement production and providing the cement types the concrete market will demand in the future.
Finally, if you need to talk to someone about cement please drop us a mail